ASTM D130 uses a visual rating system to evaluate copper corrosion caused by petroleum products. Tested copper strips are compared to a standardized reference scale, with ratings ranging from 1a (lightest tarnish) to 4c (severe corrosion). Each rating is based on specific colors indicative of corrosion. However, a common misconception is that these ratings follow a strict, stepwise progression. Instead, the classification exists within a multidimensional color scale where overlap between ratings is prevalent.
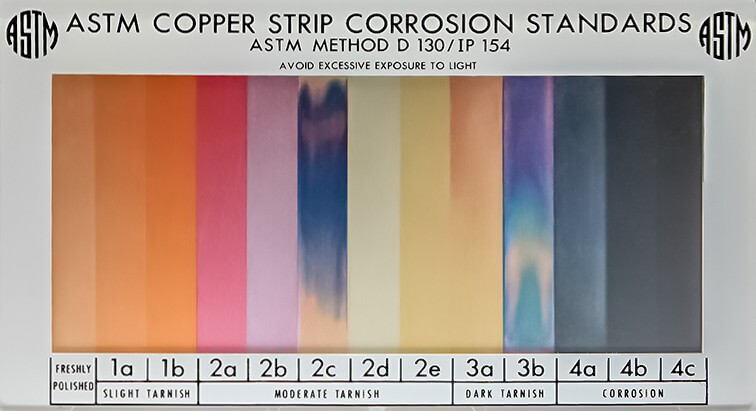
The ASTM D130 reference scale presents distinct visual classifications, which may falsely suggest a rigid, sequential progression of corrosion. However, this scale is derived from a more complex, three-dimensional color model. Corrosion colors are a product of specific sample and copper chemistry and thus do not progress in isolated steps but rather exist along a spectrum where multiple hues and intensities interact producing results almost exclusively belonging to multiple different ratings at once.
A key misunderstanding arises from the interpretation of percentage ratings in Visaya’s automated Copper Digital Detection Imaging (CuDDI) Device. These percentages do not quantify an exact transition from one classification to another but instead represent the proportion of a given color’s presence within the corrosion spectrum. Because some groups share common colors, overlap between classifications can result in readings exceeding 100%.
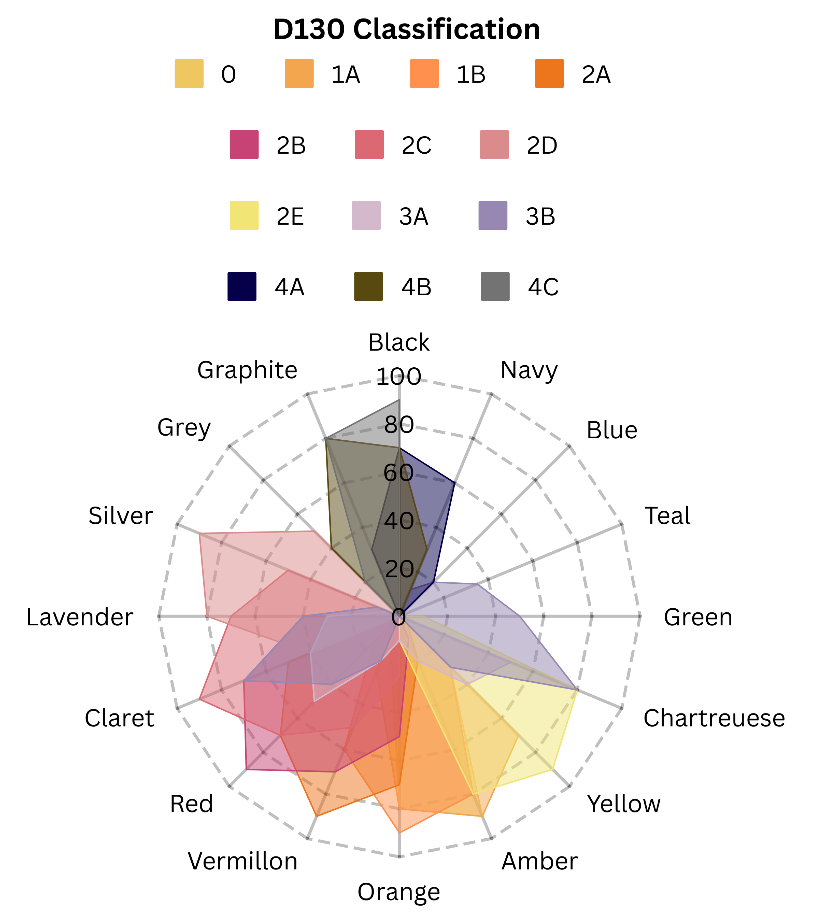
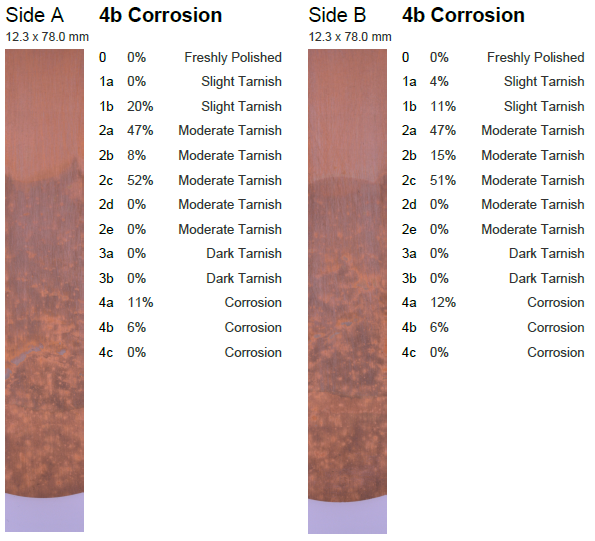
Certain classification groups display a single dominant color (monochromatic), while others
exhibit a mixture of colors (polychromatic). This impacts the ease of differentiation:
- Monochromatic Groups:
- Group 1 (Oranges): Easier to distinguish due to less color variation.
- Group 4 (Blacks/Greys): More clearly defined due to the absence of other hues.
- Polychromatic Groups:
- Group 2 (Reds, oranges, purples, silvers, yellows, greens, and absence of
greys): Significant color variation increases classification overlap. - Group 3 (Pinks, yellows, reds, and greens): The presence of multiple colors
makes transitions between ratings less distinct.
- Group 2 (Reds, oranges, purples, silvers, yellows, greens, and absence of
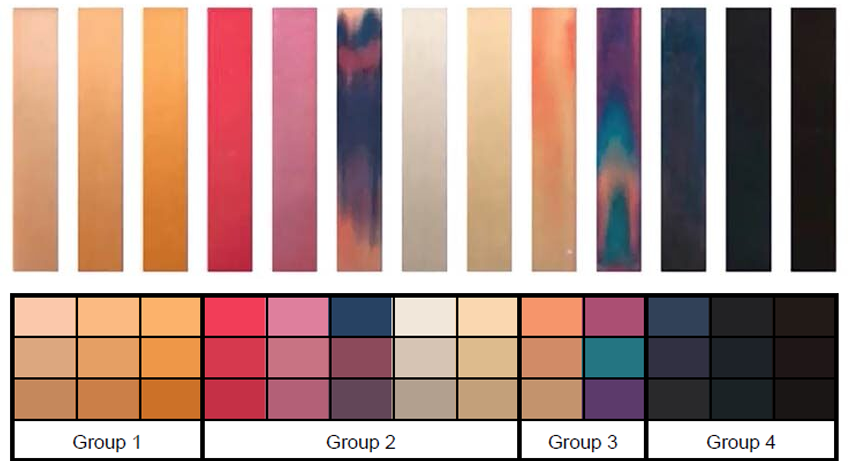
Because multiple classifications share certain colors, overlap occurs, reinforcing the need for
careful visual or digital interpretation.
Real In-House Samples
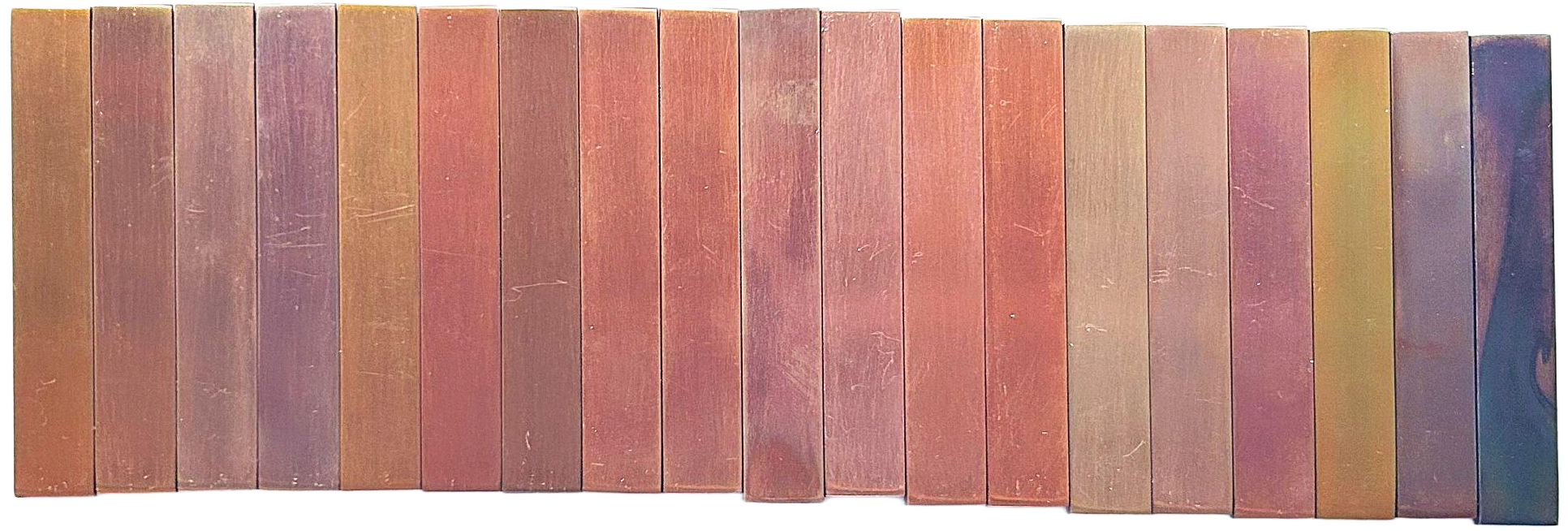
Certain corrosion ratings share color characteristics, making differentiation challenging:
- 1a to 1b: Both display slight tarnish; 1a is a very light orange tint, while 1b is slightly
darker. Lighting conditions can blur distinctions. - 1b to 2a: The transition from light tarnish to darkening is subtle, with 1b as darker
orange and 2a introducing a subtle red tint. - 2b to 3a: Brownish discoloration starts in 2b and deepens in 3a, where corrosion levels
impact clarity. - 3b to 4a: Differentiating between dark brown and early-stage severe corrosion can be
difficult, especially with uneven corrosion. - 2c to 3b, 4a to 4b: Gradual shifts from brown to black or greenish tones appear
continuous rather than sharply distinct.
The interpretation of ASTM D130 ratings is complicated by the inherent overlap of colors in corrosion classifications. Recognizing that ratings exist on a spectrum rather than as discrete steps enhances classification accuracy. When using visual or digital methods, it is crucial to consider the multidimensional nature of color interpretation to avoid misclassification. Understanding this complexity ensures a more precise evaluation of petroleum product
corrosivity and facilitates improved decision-making in corrosion analysis.