ASTM D892
Standard Test Method for Foaming Characteristics of Lubricating Oils
A precise and reliable determination of the foaming tendency of lubricant oils is a valuable diagnostic tool to optimize preventive maintenance programs of engines and machinery and reduce the enormous repair costs. Unscheduled maintenance is very costly not only in labor and materials but also in downtime. D0892 empirically rates both the foaming tendency and the foam stability of lubricants creating a big solution in the prevention of industrial machinery and equipment enhancing the process of metal wear monitoring and control.
“VISAYA FOAM-DDI analyzer is in its 2nd generation of development. The instruments by means of its unique patent pending VISION algorithm, sophisticated optics and hardware optimization, guarantees both precise, and accurate experimental results”.
Referenced Documents
ASTM Standards:
D445 Test Method for Kinematic Viscosity of Transparent and Opaque Liquids (and Calculation of Dynamic Viscosity)
D6082 Test Method for High Temperature Foaming Characteristics of Lubricating Oils
E1 Specification for ASTM Liquid-in-Glass Thermometers
E128 Test Method for Maximum Pore Diameter and Permeability of Rigid Porous Filters for Laboratory Use
E1272 Specification for Laboratory Glass Graduated Cylinders
_______________
1 This test method is under the jurisdiction of ASTM Committee D02 on Petroleum Products and Lubricants and is the direct responsibility of Subcommittee D02.06 on Analysis of Lubricants.
Terminology
Definitions:
diffuser, n—a device for dispersing gas into a fluid.
Discussion—In this test method the diffuser may be made of either metallic or non-metallic materials.
entrained air (or gas), n—in liquids, a two-phase mixture of air (or gas) dispersed in a liquid in which the liquid is the major component on a volumetric basis.
Discussion—Entrained air (or gas) may form micro size bubbles in liquids that are not uniformly dispersed and that may coalesce to form larger bubbles below or at the surface which break or form foam.
foam, n—in liquids, a collection of bubbles formed in or on the surface of a liquid in which the air or gas is the major component on a volumetric basis.
lubricant, n—any material interposed between two surfaces that reduces friction or wear between them. D6082
Discussion—In this test method, the lubricant is an oil which may or may not contain additives such as foam inhibitors.
maximum pore diameter, n—in gas diffusion, the diameter of a circular cross-section of a capillary is equivalent to the largest pore of the diffuser under consideration.
Definitions of Terms Specific to This Standard:
dynamic bubble, n—the first bubble to pass through and escape from the diffuser followed by a continuous succession of bubbles when testing for the maximum pore diameter in Annex A1.
Discussion—When a diffuser is immersed in a liquid, air can be trapped in the pores. It can escape eventually or as soon as a pressure is applied to the diffuser. When testing for maximum pore diameter (Annex A1) the escape of such bubble shall be ignored.
foam stability, n—in foam testing, the amount of foam remaining at the specified time following the disconnecting of the air supply.
Discussion—In this test method, foam stability is determined from measurements made 10 min ± 10 s after disconnecting the air supply. In cases after the air supply has been disconnected, where the foam collapses to 0 mL before the 10min settling time has elapsed, the test may be terminated and the foam stability result recorded as 0 mL.
foaming tendency, n—in foam testing, the amount of foam determined from measurements made immediately after the cessation of air flow.
Summary of Test Method
Two portions of the sample are maintained in the diffuser at two pre-established temperatures 24 ± 0.5 °C and 93.5 ± 0.5 °C. Air is blown through the sample at a controlled and constant rate of 94±5 mL/min for 5 min and allowed to settle for a period of 10 minutes. Foam height and volume is measured at the end of both periods. The tendency to foam and its stability are reported as described below in the Report Section.
Significance and Use
High surface tension contaminants in lubricants as well as air entrained in the in-use oils create bubbles and foam. Foam generates incomplete oil films, cause low oil pressures and accelerate oil degradation including additives depletion. The results are inadequate lubrication, metal ware, cavitation in pumps and altogether t comes to mechanical failures. A necessary step to minimize these effects is to have a precise and unbiased way to determine foaming characteristic in lubricant formulations so it can serve as a diagnostic tool for wearing control and for optimal PM programs of engines and machinery saving operational costs and downtime.
Apparatus
Foaming Test Apparatus, is shown in Fig. 1. It consists of a 1000-mL graduated cylinder meeting Specification E1272 class B tolerance requirement of ±6 mL and at least graduations of 10 mL. The graduated cylinder is held in position when placed in the bath, and an air-inlet tube, to the bottom of which is fastened a gas diffuser. The gas diffuser and the cylinder are manufactured following the specification of D892.
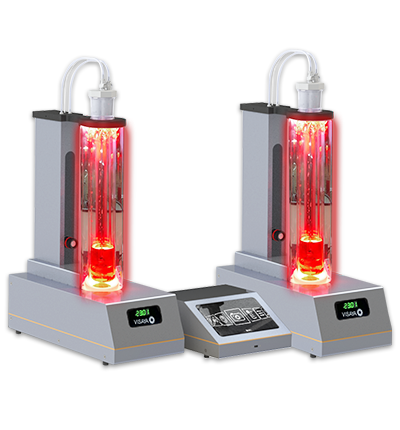
Foam Digital Detection Imaging Apparatus, Part of the total system also shown in Fig.1 consists of an apparatus for sample conditioning equipped with a high-resolution CCD camera, the reader unit which possesses a state of the art optics and the VISION algorithm that accurately determines static and dynamic foam heights after completion of the stabilization period. The high precision and accuracy of the test lies in the accurate control of temperatures, air flows and sequences in combination with the VISION algorithm analysis characterized by a minimal operator’s sample manipulation and the elimination of the critical timing involved in the manual foam height appreciation.
Test Procedure
After the thorough preparation of the apparatus shown in Fig. 1 following the procedures described in section 9 of D892, prepare the samples and stabilize them following the selected procedure described in section 10. Utilizing the patent pending FOAM-DDI analyzer, sample contained in the inserted cylinder is quickly brought to the correct test temperature with a precision of ±0.1 C.
After a predetermined soaking time, the analyzer starts flowing the air for foam production in a controlled way by means of a mass flow controller. At the 5 min mark the LED light is activated and the system VISION algorithm begins the analysis by objectively and accurately determining and displaying the foam height as illustrated in Fig.2.
Report
Foaming Tendency ASTM D892 IP 146 Foam Volume, mL, at end of 5 min blowing period |
Foaming Stability ASTM D892 IP 146 Foam Volume, mL, at end of 10 min setting period |
|
Test | ||
As received: | ||
Sequence I | ….. | ….. |
Sequence II | ….. | ….. |
Sequence III | ….. | ….. |
After Agitation: | ….. | ….. |
(Option A, 9.5.1) | ….. | ….. |
Sequence I | ….. | ….. |
Sequence II | ….. | ….. |
Sequence III | ….. | ….. |
Precision and Bias
The Precision Study and Supporting Data for D892 were submitted to ASTM International Headquarters under two research reports: RR D02 – 1007 and RR:D02-1244.
Repeatability—The difference between two test results obtained by the same operator with the same apparatus under constant operating conditions on identical test material would, in the long run, in the normal and correct operation of the test method, provide the following repeatability value:
Sequence | Repeatability |
I | 0.10 (x + 55) |
II | 0.10 (x + 44) |
III | 0.15x |
Reproducibility—Taken as the difference between two single and independent test results obtained by different operators working in different laboratories on identical test material would, in the long run, in the normal and correct operation of the test method, exceed the following values in only one case in twenty:
Sequence | Repeatability |
I | 0.29 (x + 55) |
II | 0.26 (x + 44) |
III | 0.44x |
Bias— The same Research Report reports noted the no availability of a suitable accepted reference material to determine bias for D892.
The 2nd Generation FoamDDI has been subjected to a series of hardware modifications to optimize the cooling and heating process and to solve several ambiguities due to sample preparation, temperature probe location among others remaining in the current standard.
The new patent-pending FoamDDI eliminates the need for sample manipulation and critical timing measurement as in the case of manual foam height determinations. Using a patent pending heating and cooling system with a vision algorithm and automation, the FoamDDI, records, calculates and displays repeatable and accurate results with no operation bias in minutes!
Check out the FoamDDI here.